Balancing axial force in multistage centrifugal pumps is a critical technology to ensure stable operation. Due to the series arrangement of impellers, axial forces accumulate significantly (up to several tons). If not properly balanced, this can lead to bearing overload, seal damage, or even equipment failure. Below are common axial force balancing methods, along with their principles, advantages, and disadvantages.
1. Symmetrical Impeller Arrangement (Back-to-Back / Face-to-Face)
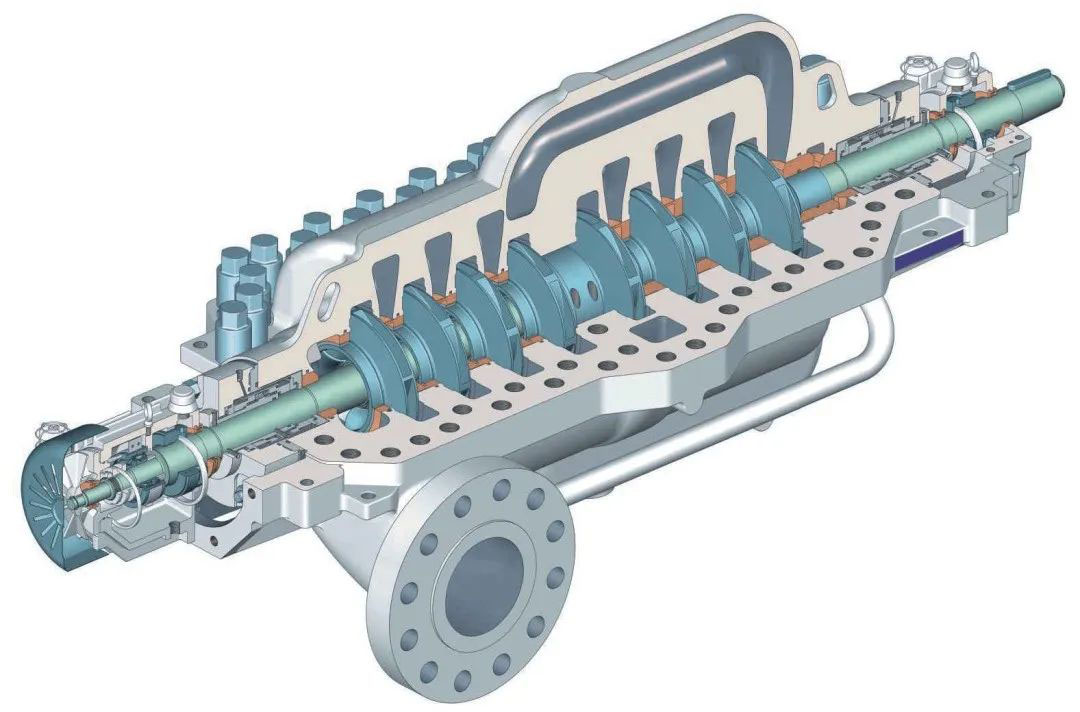
In the design of the axial force balance device of modern centrifugal pump, the impeller stage is generally selected as an even number, because when the impeller stage is an even number, the impeller symmetrical distribution method can be used to balance the axial force of the equipment, and the axial force generated by the symmetrically distributed impeller in the operation process is equal in magnitude and opposite in direction, and it will show a equilibrium state on the macroscopic level. In the process of design, it should be noted that the sealing throttling size before the inlet of the reverse impeller is consistent with the diameter of the impeller to ensure good sealing.
● Principle: Adjacent impellers are arranged in opposite directions so that their axial forces cancel each other out.
● Back-to-back: Two sets of impellers are installed symmetrically around the pump shaft midpoint.
● Face-to-face: Impellers are arranged facing inward or outward in a mirrored configuration.
● Advantages: No additional devices required; simple structure; high balancing efficiency (over 90%).
● Disadvantages: Complex pump housing design; difficult flow path optimization; only applicable to pumps with an even number of stages.
● Applications: High-pressure boiler feed pumps, petrochemical multistage pumps.
2. Balancing Drum
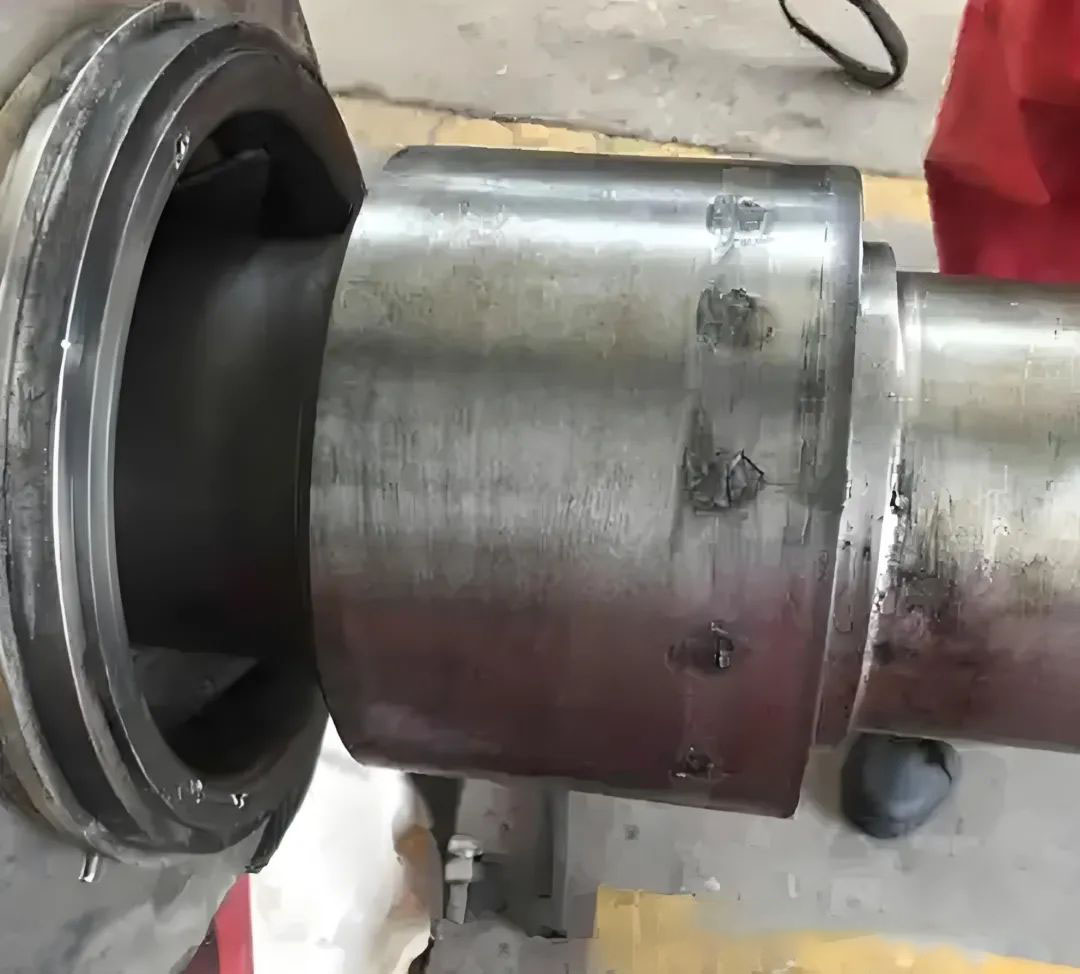
The balance drum structure (also known as the balance piston) does not have a tight axial running clearance, which can compensate for most of the axial thrust, but not all of the axial thrust, and there is no additional compensation when moving in the axial position, and thrust bearings are generally required. This design will have higher internal recirculation (internal leakage) but is more tolerant of start-ups, shutdowns, and other transient conditions.
● Principle: A cylindrical drum is installed after the last-stage impeller. High-pressure fluid leaks through the gap between the drum and casing into a low-pressure chamber, generating a counteracting force.
● Advantages: Strong balancing capability, suitable for high-pressure, multistage pumps (e.g., 10+ stages).
● Disadvantages: Leakage losses (~3–5% of flow rate), reducing efficiency. Requires additional balancing pipes or recirculation systems, increasing maintenance complexity.
● Applications: Large multistage centrifugal pumps (e.g., long-distance pipeline pumps).
3. Balancing Disk
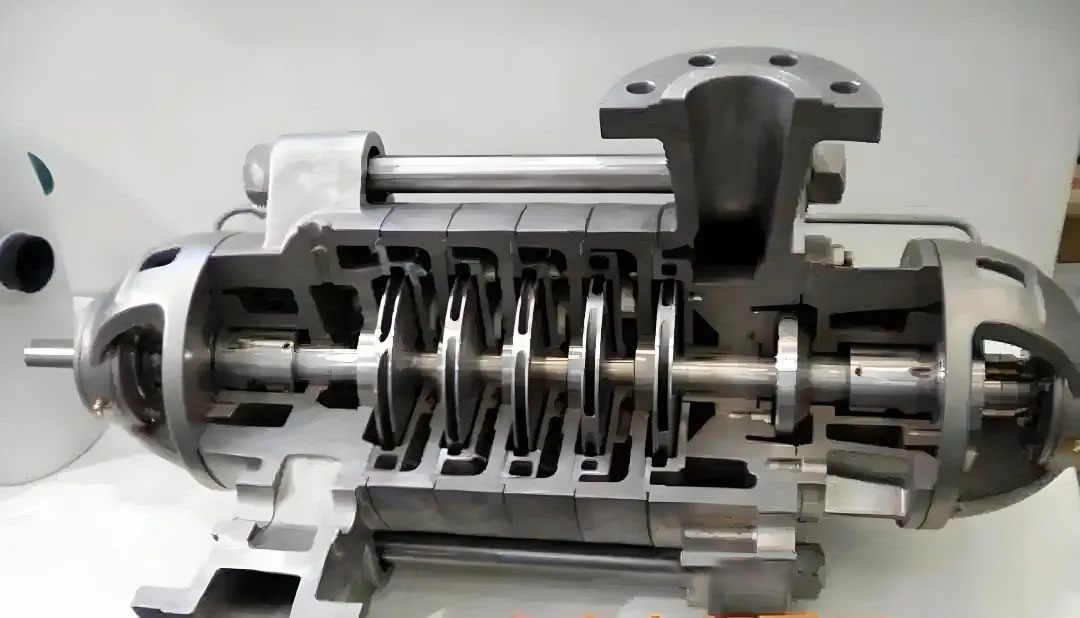
As a common design method in the design process of the axial force balance device of modern multistage centrifugal pump, the balance disc method can be moderately adjusted according to the production demand, and the balance force is mainly generated by the cross-section between the radial clearance and the axial clearance of the disk, and the other part is mainly generated by the axial clearance and the outer radius section of the balance disc, and these two balancing forces play the role of balancing the axial force. Compared with other methods, the advantage of the balance plate method is that the diameter of the balance plate is larger and the sensitivity is higher, which effectively improves the operation stability of the equipment device. However, due to the small axial running clearance, this design is susceptible to wear and damage under transient conditions.
● Principle: A movable disk is installed after the last-stage impeller. The pressure difference across the disk dynamically adjusts its position to counteract axial force.
● Advantages: Automatically adapts to axial force variations; high balancing precision.
● Disadvantages: Friction causes wear, requiring periodic replacement. Sensitive to fluid cleanliness (particles can jam the disk).
● Applications: Early-stage multistage clean-water pumps (gradually being replaced by balancing drums).
4. Balancing Drum + Disk Combination
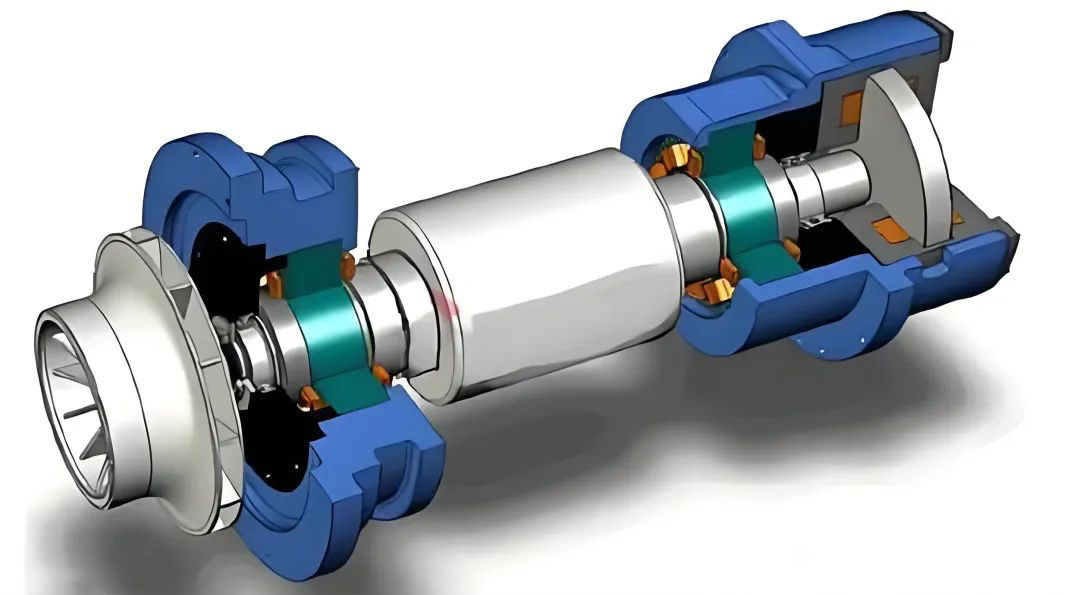
Compared with the balance plate method, the balance plate drum method is different in that the size of its throttle bushing part is larger than the size of the impeller hub, while the balance disc requires the size of the throttle bushing to correspond to the size of the impeller hub. Generally speaking, in the design method of the balance plate drum, the balance force generated by the balance plate accounts for more than half of the total axial force, and the maximum can reach 90% of the total axial force, and the other parts are mainly provided by the balance drum. At the same time, moderately increasing the balance force of the balance drum will correspondingly reduce the balance force of the balance plate, and correspondingly reduce the size of the balance plate, thereby reducing the wear degree of the balance plate, improving the service life of the equipment parts, and ensuring the normal operation of the multistage centrifugal pump.
● Principle: The drum handles most of the axial force, while the disk fine-tunes the residual force.
● Advantages: Combines stability and adaptability, suitable for variable operating conditions.
● Disadvantages: Complex structure; higher cost.
● Applications: High-performance industrial pumps (e.g., nuclear reactor coolant pumps).
5. Thrust Bearings (Auxiliary Balancing)
● Principle: Angular contact ball bearings or Kingsbury bearings absorb residual axial force.
● Advantages: Reliable backup for other balancing methods.
● Disadvantages: Requires regular lubrication; shorter lifespan under high axial loads.
● Applications: Small-to-medium multistage pumps or high-speed pumps.
6. Double-Suction Impeller Design
● Principle: A double-suction impeller is used at the first or intermediate stage, balancing axial force through dual-side inflow.
● Advantages: Effective balancing while improving cavitation performance.
● Disadvantages: Only balances single-stage axial force; other methods are needed for multistage pumps.
7. Hydraulic Balance Holes (Impeller Backplate Holes)
● Principle: Holes are drilled in the impeller backplate, allowing high-pressure fluid to recirculate to the low-pressure zone, reducing axial force.
● Advantages: Simple and low-cost.
● Disadvantages: Reduces pump efficiency (~2–4%). Only suitable for low axial force applications; often requires supplementary thrust bearings.
Comparison of Axial Force Balancing Methods
Method | Efficiency | Complexity | Maintenance Cost | Typical Applications |
Symmetrical Impellers | ★★★★★ | ★★★ | ★★ | Even-stage high-pressure pumps |
Balancing Drum | ★★★★ | ★★★★ | ★★★ | High-head multistage pumps |
Balancing Disk | ★★★ | ★★★★ | ★★★★ | Clean fluids, variable loads |
Drum + Disk Combo | ★★★★★ | ★★★★★ | ★★★★ | Extreme conditions (nuclear, military) |
Thrust Bearings | ★★ | ★★ | ★★★ | Residual axial force balancing |
Double-Suction Impeller | ★★★★ | ★★★ | ★★ | First or intermediate stage |
Balance Holes | ★★ | ★ | ★ | Small low-pressure pumps |
Post time: Mar-29-2025