Centrifugal Pump Seal Basics
Centrifugal pumps are widely used in various industries, including oil and gas, chemical processing, water treatment, and power generation, to transport fluids efficiently. One of the critical components of a centrifugal pump is the sealing system, which prevents leakage of the pumped fluid and ensures the pump operates safely and efficiently. Among the different types of sealing systems, double mechanical seals are commonly employed in applications where leakage prevention is paramount. However, high temperatures can pose significant challenges to the integrity of double seal systems, potentially leading to dangerous increases in pressure and catastrophic failures.
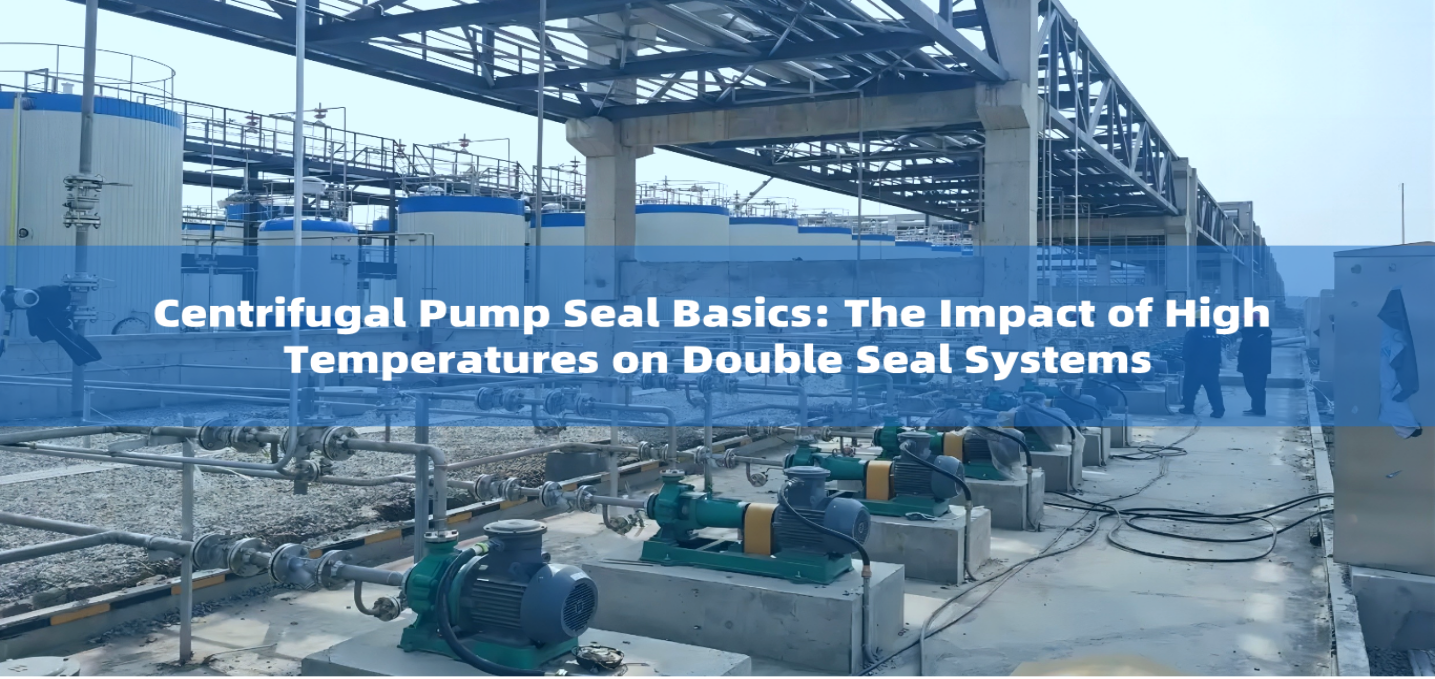
Basics of Centrifugal Pump Seals
Mechanical seals are the most common type of sealing system used in centrifugal pumps. They consist of two primary components: a stationary seal face and a rotating seal face, which are pressed together to create a tight seal. The seal faces are typically made of durable materials such as carbon, ceramic, or silicon carbide, which can withstand the harsh conditions inside the pump. The primary purpose of the seal is to prevent the pumped fluid from leaking out of the pump casing while also keeping contaminants from entering the system.
In single mechanical seal systems, one set of seal faces is used to contain the fluid. However, in applications involving hazardous, toxic, or high-pressure fluids, a double mechanical seal system is often employed. Double seals consist of two sets of seal faces arranged in tandem or back-to-back configuration, with a barrier fluid between them. This design provides an additional layer of protection against leakage and enhances the reliability of the sealing system.
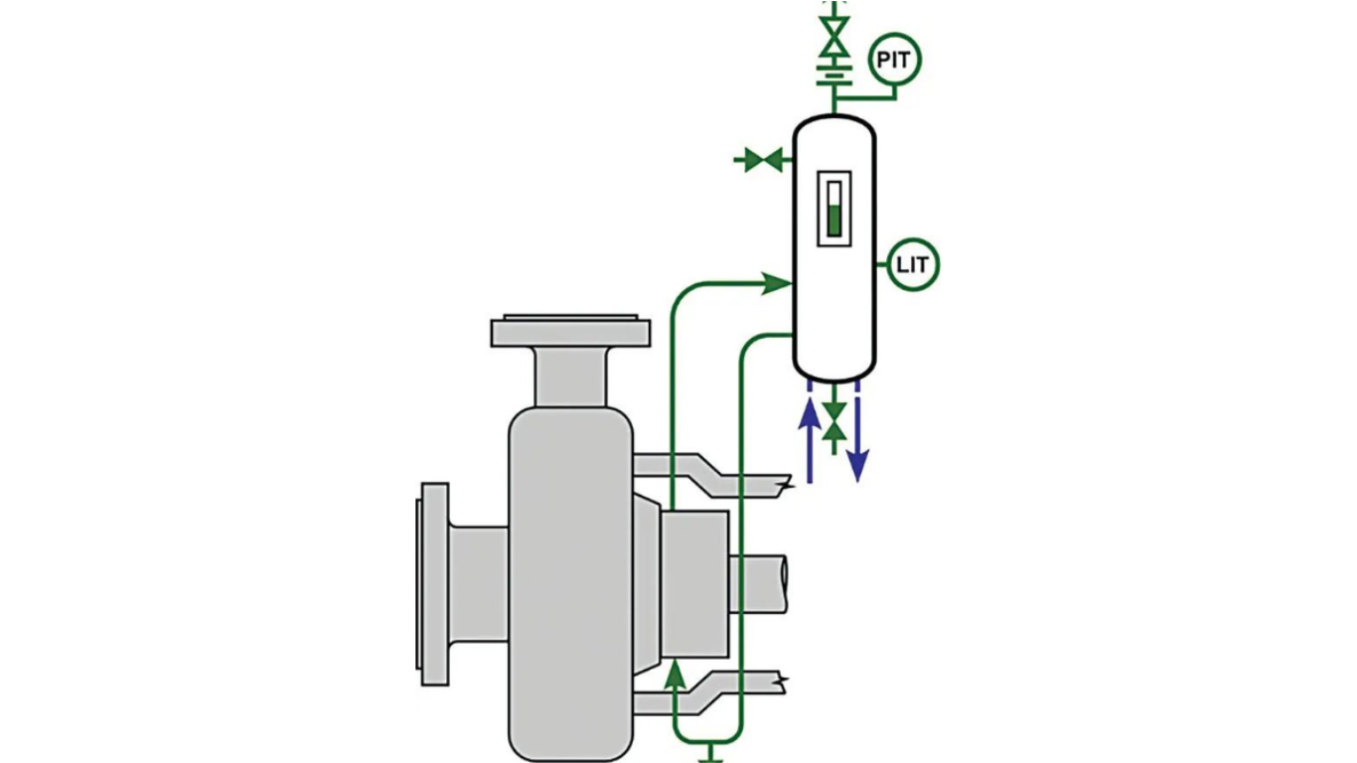
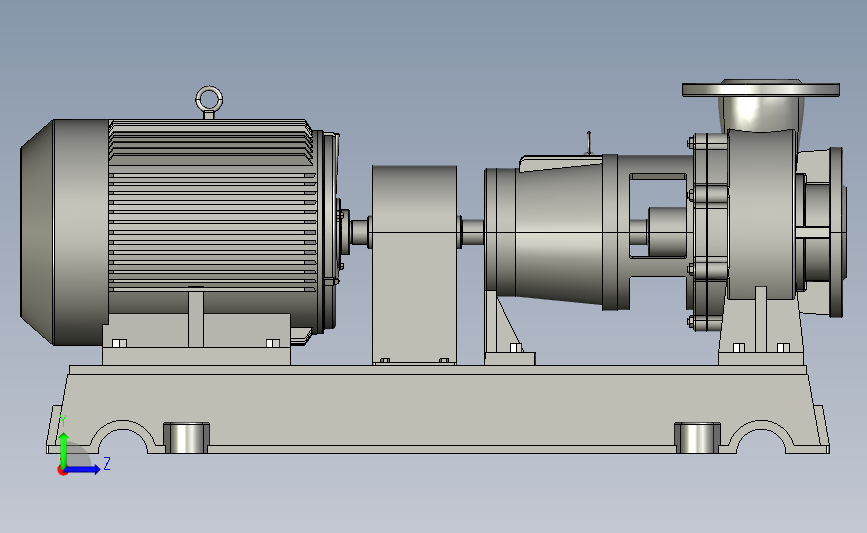
Double Seal Systems and Their Advantages
Double mechanical seals are particularly advantageous in applications where leakage prevention is critical. The barrier fluid between the two sets of seal faces acts as a buffer, preventing the pumped fluid from escaping into the environment. Additionally, the barrier fluid helps to lubricate and cool the seal faces, reducing wear and extending the life of the seals. Double seals are commonly used in applications involving high pressures, high temperatures, corrosive fluids, or fluids that are environmentally hazardous.
There are two main types of double seal configurations:
Tandem Seals: In this configuration, the primary seal faces the pumped fluid, while the secondary seal acts as a backup in case the primary seal fails. The barrier fluid is typically maintained at a pressure lower than the pumped fluid to ensure that any leakage flows inward toward the pump.
Back-to-Back Seals: In this arrangement, the two sets of seal faces are oriented in opposite directions, with the barrier fluid maintained at a pressure higher than the pumped fluid. This configuration is often used in applications involving volatile or hazardous fluids.
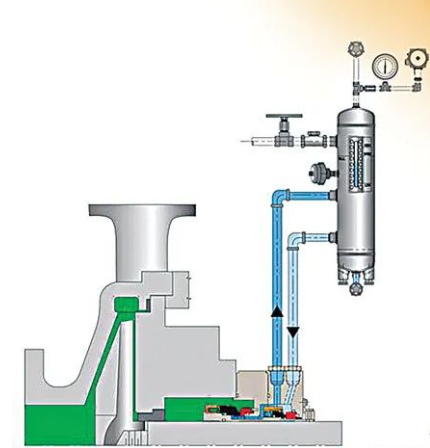
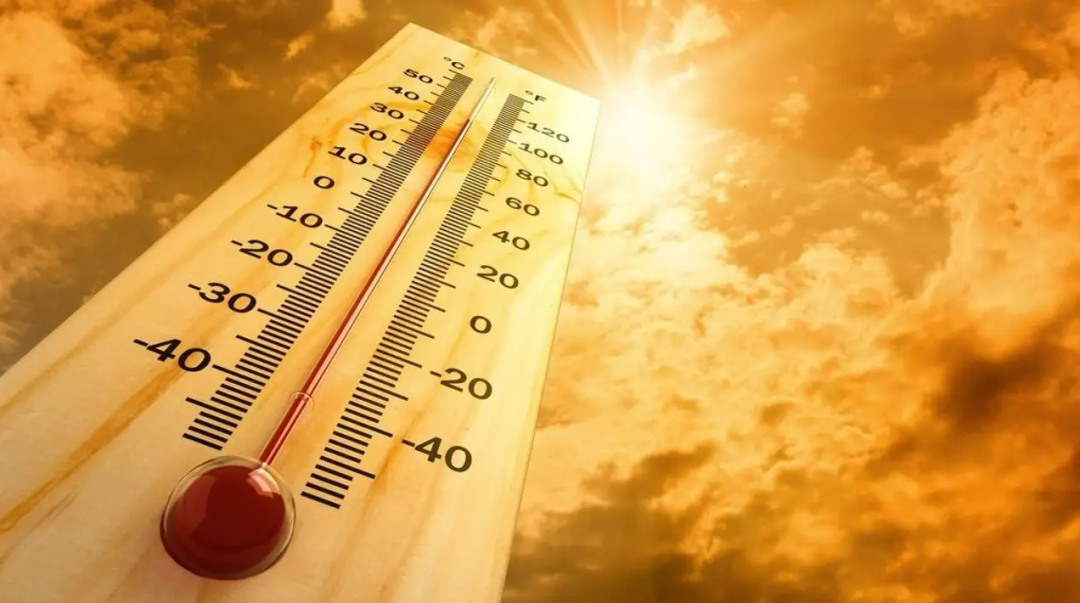
The Impact of High Temperatures on Double Seal Systems
While double seal systems offer significant advantages, they are not immune to the challenges posed by high temperatures. High temperatures can arise from various sources, including the pumped fluid, the operating environment, or friction between the seal faces. When temperatures rise, several issues can occur that compromise the integrity of the seal system:
Thermal Expansion: High temperatures cause the materials in the seal faces and other components to expand. If the thermal expansion is not uniform, it can lead to misalignment of the seal faces, resulting in increased leakage or seal failure.
Increased Pressure in the Barrier Fluid: In a double seal system, the barrier fluid is critical for maintaining the seal's integrity. However, high temperatures can cause the barrier fluid to expand, leading to a dangerous increase in pressure within the seal chamber. If the pressure exceeds the design limits of the seal system, it can cause the seals to fail, resulting in leakage or even catastrophic damage to the pump.
Degradation of Seal Materials: Prolonged exposure to high temperatures can cause the materials used in the seal faces to degrade. For example, elastomers used in O-rings or gaskets may harden or crack, while carbon or ceramic seal faces may become brittle. This degradation can compromise the seal's ability to maintain a tight barrier, leading to leakage.
Vaporization of the Barrier Fluid: In extreme cases, high temperatures can cause the barrier fluid to vaporize, creating gas pockets within the seal chamber. These gas pockets can disrupt the lubrication and cooling of the seal faces, leading to increased friction, wear, and eventual seal failure.
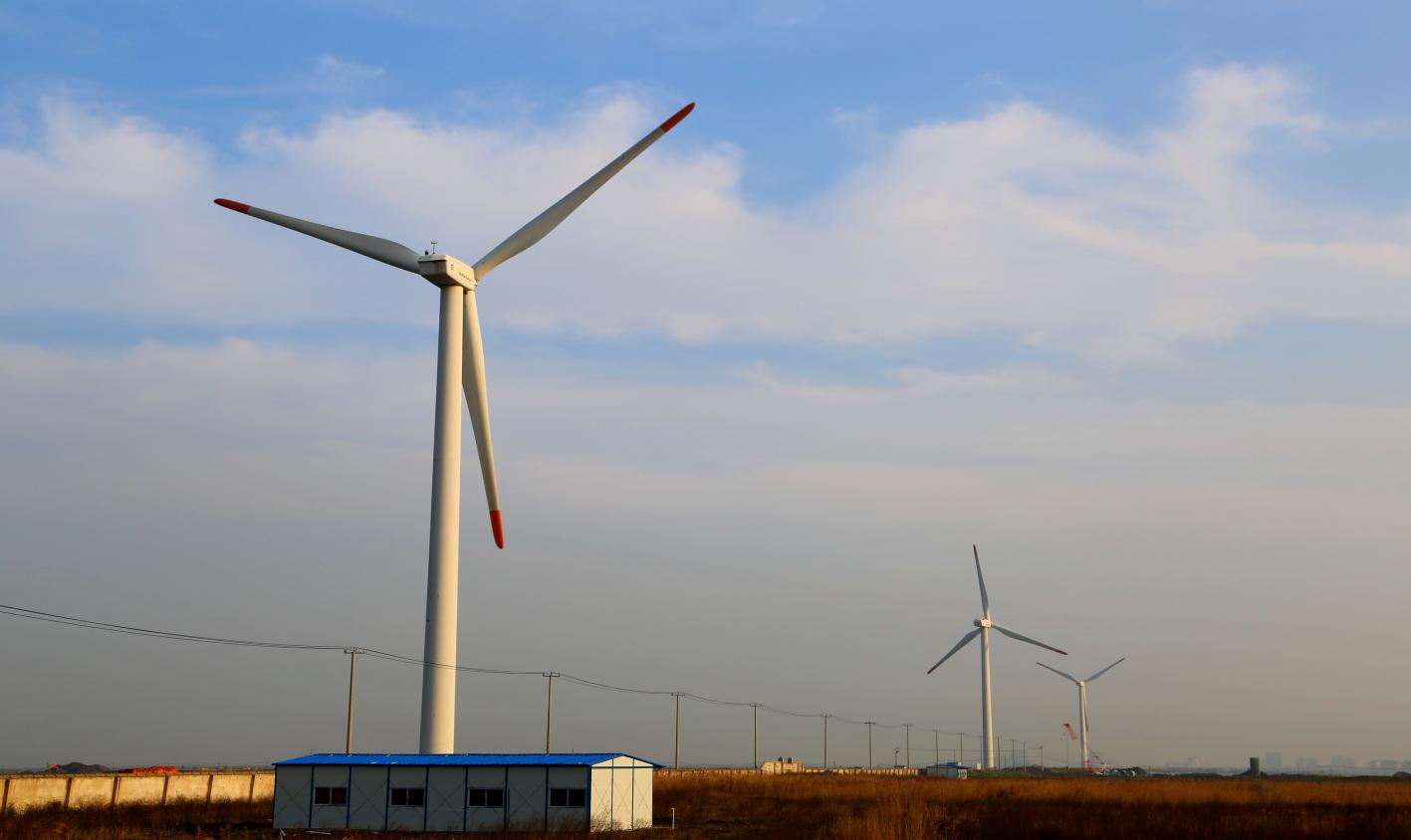
Mitigating the Risks of High Temperatures
To prevent the adverse effects of high temperatures on double seal systems, several measures can be taken:
Proper Material Selection: Choosing seal materials that can withstand high temperatures is critical. For example, high-temperature elastomers such as fluorocarbon or perfluoroelastomer (FFKM) can be used for O-rings, while advanced ceramics or silicon carbide can be used for seal faces.
Check the balance ratio:Choosing a seal designed for high isolation liquid pressure on the primary seal.
Cooling Systems: Installing cooling systems, such as heat exchangers or cooling jackets, can help to dissipate heat and maintain the temperature of the barrier fluid within safe limits.
Pressure Management: Monitoring and controlling the pressure of the barrier fluid is essential to prevent dangerous pressure increases. Pressure relief valves or pressure control systems can be installed to maintain the barrier fluid at the optimal pressure.
Regular Maintenance: Regular inspection and maintenance of the seal system can help to identify and address issues before they lead to failure. This includes checking for signs of wear, misalignment, or degradation of seal materials.
Conclusion
TKFLO centrifugal pump seals, particularly double mechanical seals, play a vital role in ensuring the safe and efficient operation of pumps in demanding applications. However, high temperatures can pose significant risks to the integrity of double seal systems, leading to increased pressure, material degradation, and potential seal failure. By understanding the basics of centrifugal pump seals and implementing appropriate measures to mitigate the effects of high temperatures, operators can enhance the reliability and longevity of their pump systems. Proper material selection, cooling systems, pressure management, and regular maintenance are all essential components of a robust strategy to address the challenges posed by high temperatures in double seal systems.
Post time: Mar-17-2025