Centrifugal pumps are widely utilized across various industries as essential fluid transport equipment. Their operational efficiency directly impacts both energy utilization and equipment reliability. However, in practice, centrifugal pumps often fail to reach their theoretical peak efficiency. This shortfall results from a combination of design limitations, operational variances, maintenance issues, and external environmental factors.
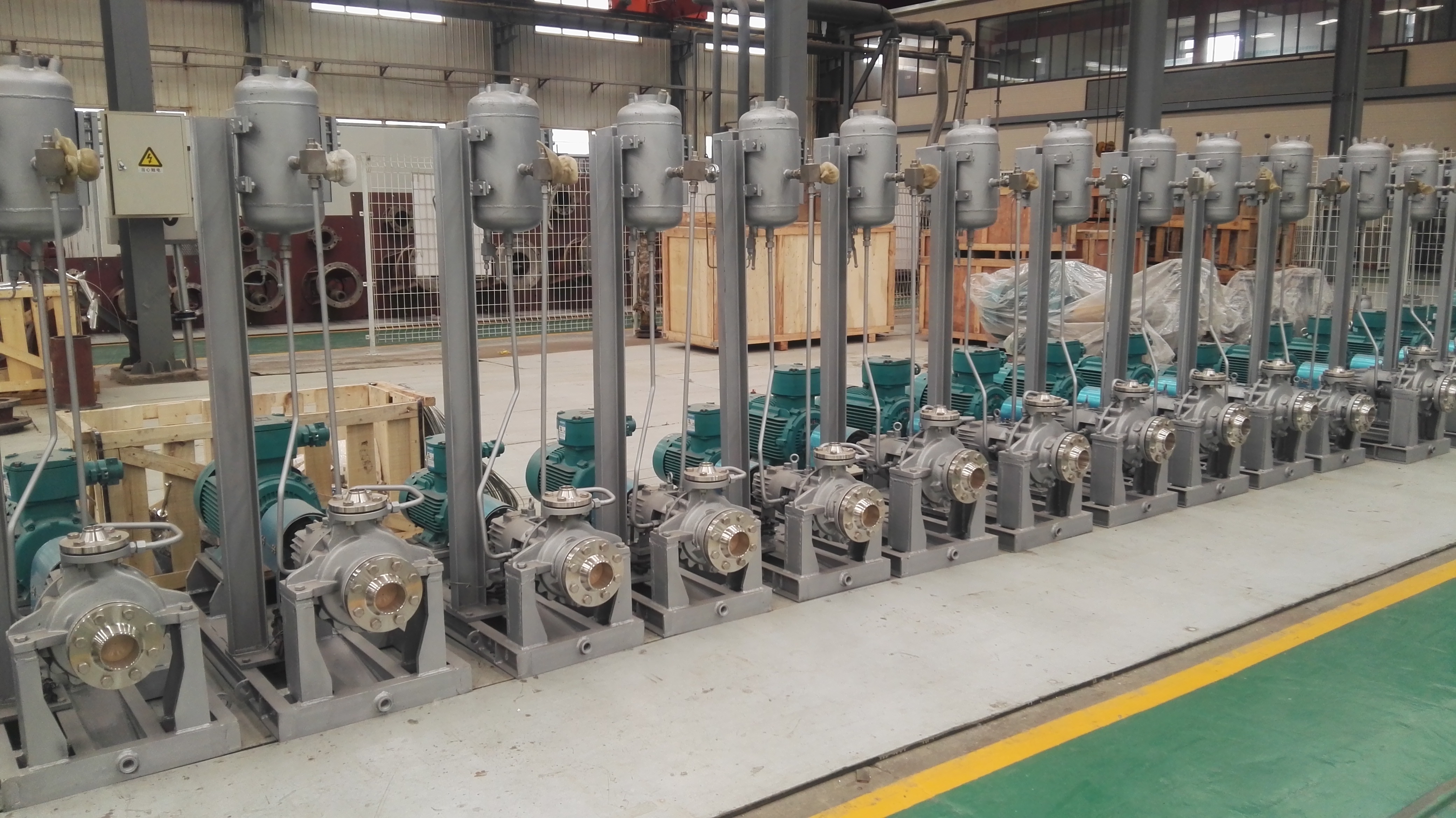
Understanding Centrifugal Pump Efficiency
To effectively analyze the factors affecting pump efficiency, it's important to first understand its composition. The overall efficiency of a centrifugal fire pump is typically determined by three key components:
Hydraulic Efficiency – Represents energy losses due to fluid dynamics within the pump.
Mechanical Efficiency – Refers to losses from friction and mechanical movement.
Volumetric Efficiency – Accounts for losses caused by internal leakage of the fluid.
The interplay between these components defines the total operational efficiency of the pump.
Key Factors Influencing Centrifugal Pump Efficiency
1. Hydraulic Design Factors
The hydraulic design significantly influences how efficiently fluid moves through the pump:
Impeller Design As the core component, the impeller’s geometry—including diameter, blade number, inlet/outlet angles, and curvature—directly affects flow characteristics and energy conversion efficiency.
Volute Design The volute collects fluid discharged from the impeller and converts kinetic energy into pressure energy. Poor design, especially excessive diffusion angles, can cause eddies and secondary flows, increasing hydraulic losses.
Seal Design Seal clearances impact both leakage and friction losses. Excessive clearance leads to leakage, while minimal clearance can increase friction and wear.
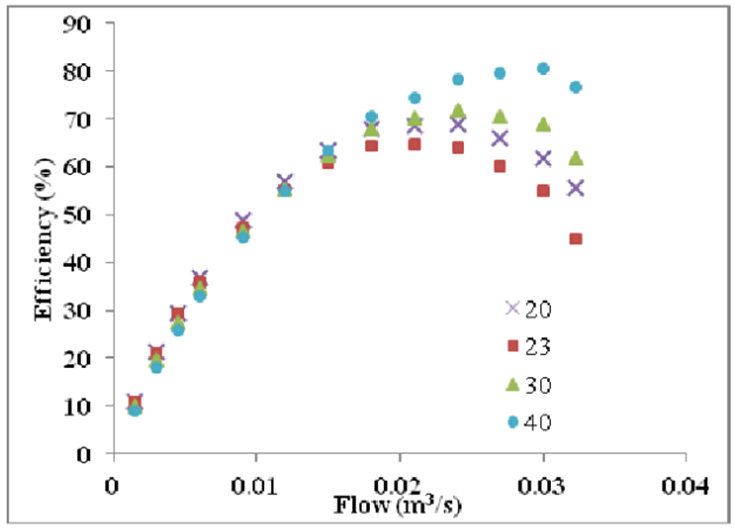
2. Operating Conditions
Deviation from design specifications can drastically affect performance:
Off-Design Operation Pumps are designed to operate at a Best Efficiency Point (BEP). Operating significantly away from this point results in increased hydraulic losses and reduced efficiency.
Cavitation When pressure at the suction side drops below the liquid's vapor pressure, vapor bubbles form and collapse within the impeller, damaging components and reducing efficiency.
3. Mechanical Loss Factors
Mechanical losses originate from internal friction and component wear:
Bearing and Seal Friction Friction at seals and bearings is a major contributor to energy loss. Using high-performance, low-friction materials can mitigate this.
Balancing Device Losses Multistage pumps often employ balancing devices to counter axial thrust. Improper design or wear can introduce additional energy losses.
Seal Leakage Over time, seals may deteriorate, leading to fluid leakage and a reduction in volumetric efficiency.
4. Maintenance-Related Issues
Ongoing maintenance is critical to sustaining performance:
Impeller and Volute Wear Continuous operation leads to wear and erosion of internal surfaces, increasing hydraulic resistance and losses.
Increased System Resistance Fouling or clogging within pipes increases flow resistance, reducing overall pump efficiency.
Shaft Misalignment Poor alignment between the pump shaft and driver can induce vibration, elevate mechanical losses, and reduce service life.
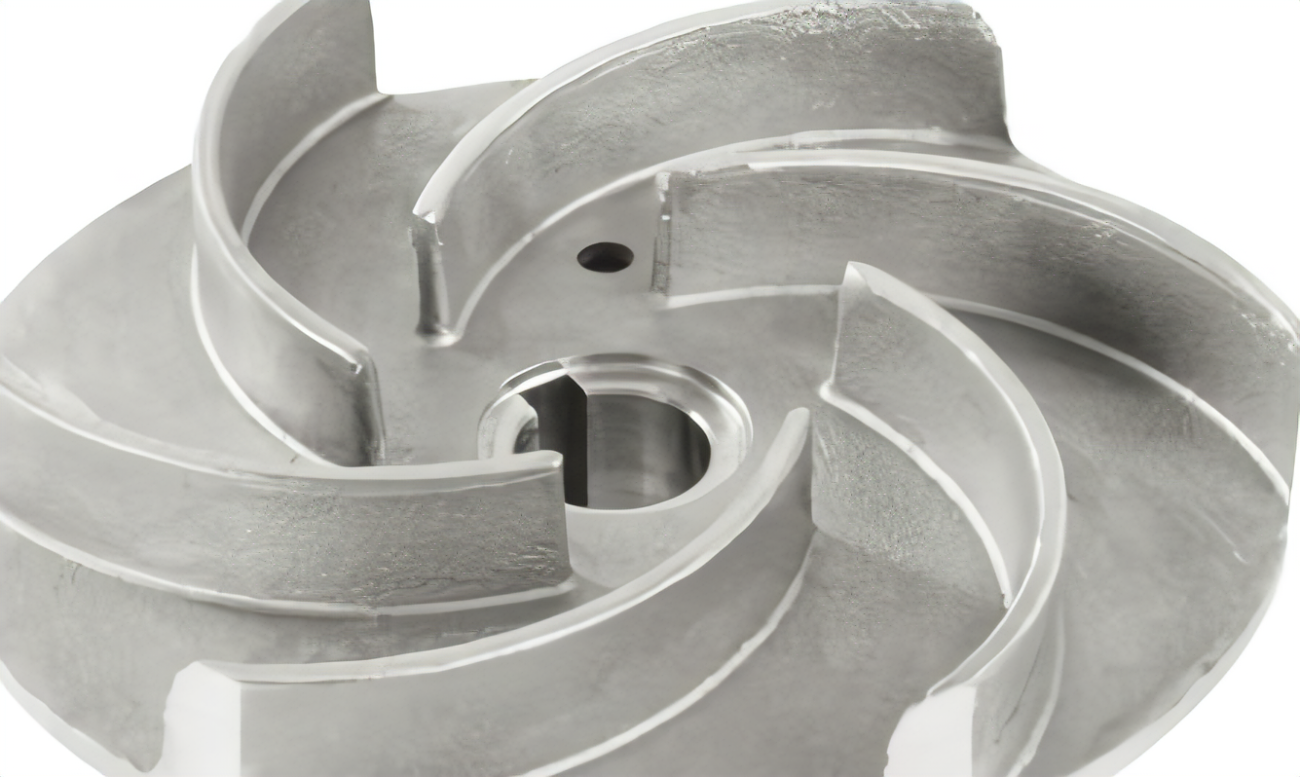
5. Environmental Factors
External conditions also influence pump efficiency:
Fluid Viscosity Higher viscosity increases flow resistance, reducing efficiency.
Solids Content Fluids with suspended solids cause increased wear and flow obstruction, leading to efficiency drops.
Ambient Temperature Temperature affects both fluid properties and the performance of lubrication systems, impacting overall efficiency.
Strategies to Improve Centrifugal Pump Efficiency
To enhance the efficiency and reliability of centrifugal pumps, consider the following approaches:
Optimized Design Use computational fluid dynamics (CFD) to simulate internal flow patterns and optimize the impeller and volute for minimal hydraulic losses.
Proper Pump Selection and Control Ensure pumps operate near their design point. Use variable frequency drives (VFDs) to adjust speed based on demand, and consider using multiple pumps in parallel to match load fluctuations efficiently.
Regular Maintenance Implement a proactive maintenance schedule. Clean internal surfaces, replace worn parts, and monitor conditions using techniques such as vibration analysis and temperature tracking.
Adapt to Environmental Conditions Select pump types that are compatible with the properties of the handled fluid. Where possible, manage ambient conditions to minimize their impact on performance.
Conclusion
The efficiency of centrifugal pumps is influenced by a wide range of interconnected factors. By addressing hydraulic design, aligning operational parameters, maintaining mechanical components, and managing environmental impacts, substantial improvements in pump performance and energy savings can be achieved. A comprehensive, proactive approach is key to maximizing the long-term efficiency and reliability of centrifugal pump systems.
Post time: Apr-24-2025